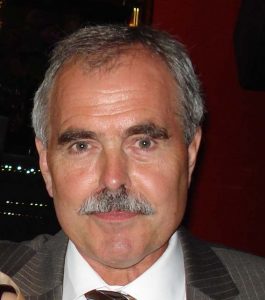
John Pepper, director, ColemSpice, highlights the key elements involved in designing and future-proofing the control room of a teleport.
Designing a control room requires above all proper planning. It takes time to do it properly, but in fact it will save the operator time and money in the long run. A well-designed and properly future-proofed space will adapt seamlessly to new technology and physical expansion, if required, without costly refurbishment and interruption to operations.
Certainly, I have always stressed the importance of preliminary survey investigation to provide the electrical and mechanical teams with a comprehensive overview and schedule of condition, to produce the correct engineering design solutions. The HVAC and lighting systems should have control sytems that can be adjusted to react to the changing needs of the operators’ “24-hour body clock”, yet maintain a consistent working environment.
Whenever faced with the start of a new project, there are four key stages to follow:
Clarification: Spelling out the clients’ operational brief
This stage is about clarifying the clients’ operational brief and know exactly what is expected from the installation. Every project is different and has different requirements depending on whether it is a new concrete shell or an existing operation with legacy equipment that needs to be to be integrated with new systems and processes. Therefore, each installation will be approached differently and needs to begin with structured client meetings where we can co-ordinate, process and produce a comprehensive set of requirements for that project setting out milestones, dates and objectives.
Analysis and problem definition: Getting the larger team on board
Any professional team installing a system on this scale will need to project manage a large team of installers and specialist suppliers, as well as electrical and HVAC engineers, including, in some scenarios, local architects and structural professionals. I believe it is vital to involve all of these professionals in infrastructure and design meetings from the start, to get their input, and also ensure everyone is on board with the project in hand.
These meetings will be used to analyse the project and its challenges, as well as to assemble all the information with regard to power and data cable feeds, and to prepare a draft infrastructure plan based on the clients’ equipment asset schedule, which will provide a check-list for “day one” requirements and also future expansion.
[boxposthighlight]
Detailed design
Before any installation work can begin, the entire project needs to be captured in an extremely detailed design package, covering acoustics, access control and physical measures, to counter security risks.
Cabling – Naturally control rooms include a lot of rack-mounted equipment, meaning a vast array of cabling. Future proofing is critical for further equipment, that may be installed at a future date. Therefore, it is important to audit and process all cable services to produce infrastructure layouts for the control room, including under-floor cabling routing and segregation for power distribution, incoming services, power /data redundancy and general electrical and mechanical performance specifications.
General arrangement layouts -Once the cabling infrastructure has been decided, it is vital to plan the overall internal feasibility layouts. This involves looking at everything from console configuration, back office support areas, safety issues,
Consoles – The next stage is the design and development of the console through to equipment audit, simulation trials, working drawings, budgeting, procurement and site installation and commissioning.
Lighting – Lighting is often overlooked in control room installations, however getting this right is vital. Bearing in mind that operators will be spending long hours looking at screens, the lighting must be as perfect as possible to ensure they can do their job comfortably. Therefore, this should be included as a key part of the design process, with working drawings, specification of fittings, and budgeting before work commences.
Walls and ceilings – Another key consideration is acoustics. The hard surface finishes will need acoustic treatment to reduce effects of noise reflection, which can be mitigated by various applied acoustic panel applications. Potential vibration noise from supply and air return ducting needs to be reviewed and fans may need to be insulated to minimise equipment or air turbulence noise.
[/boxposthighlight]Implementation and operational feedback
Only once all the above has been completed and planned should the implementation begin. If the planning has been done well, the installation itself should run smoothly, however it doesn’t stop there. Receiving feedback once the control room is up and running is vital to flag any issues, which can then be resolved.
Designing a control room requires a unique combination of cutting edge design and practical knowledge. Understanding how a control room functions and the daily demands of the people working there is vital to developing an efficient teleport facility.
Add Comment