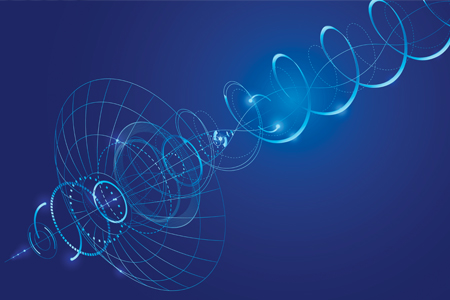
A number of new trends are shaping the future of satellite technology, and they are in the spotlight of research labs around the world. This article summarises some of these technologies, focusing on the future of RF/microwave passive components.
Satellite payloads have had fixed features until now, and a flexible allocation of resources is not usually easy or even possible. Future satellites demand this flexibility, in order to adapt to changes in bandwidth, use available resources efficiently or simply modify initial functionality.
In general, the remote reconfiguration of a flexible payload will be a feature of next-gen satellites, seamlessly accommodating future (unknown) needs. Onboard traffic routing can be done using reconfigurable switch matrices based on mechanical, ferrite and semiconductor technologies.
In recent years, multiple studies have been performed to increase the maturity level of RF-MEMS (microelectromechanical systems). RF-MEMS benefit from reduced size, low power consumption and linear operation at high frequencies. Reconfigurable microwave geometries can be implemented, using micromachining and integrated MEMS actuators.
However, RF-MEMS developers have part reliability difficulties, a key parameter when considering hardware for space systems. New technologies such as Phase Change Materials (PCM) are providing promising results for broadband, low-loss, low-power and very compact RF switch solutions.
On the other hand, other approaches such as SIW (Substrate Integrated Waveguide) combine the advantages of waveguides (low-loss and medium-power operation) with those of planar circuits (low cost) and have also been proposed for reconfigurable circuits in space.
Although there have been great advances in this area of reconfigurable satellite circuits, flexible frequency-agile satellite front-ends require compact, high quality factor, tunable resonators and filters. Unfortunately, these are not easy to design and fabricate, as high quality factor, tunability and high compactness are not easily compatible within the same device.
Future large space-based satellite networks will deliver high data rate services for high-quality internet connections around the globe – at least, this is the plan. Companies intend to provide a network that connects sensors globally, enabling disruptive IoT applications even in the most remote locations.
In this new Internet of Space (IoS) era, data, sensors and space are interlaced more than ever. This network of interconnected satellites (with both ground stations on Earth and among each other, sometimes using optical links) may take the form of constellations of hundreds of low-cost LEO satellites, allowing resilient, reliable and secure communications, as well as a significant reduction of launch costs. You can check the latest news on SpaceX Starlink or Airbus OneWeb projects, among others.
Smaller technology demonstration constellations are also being launched or planned in the area of Earth observation, most of the time in conjunction with universities. The common challenge is designing reliable payloads of small size and weight, low power consumption and low cost.
Additive Manufacturing (AM) applied to space appeared some years ago as an enabling technology for RF/microwave devices and IoS. AM actually comprises different techniques, each with pros and cons.
In the context of RF/microwave, some of the most promising technologies are fused deposition modelling (FDM) of polymers, polymer and ceramic stereo-lithography (SLA), and selective laser melting (SLM) of metals. SLM is very attractive in the sense that the printed part is already metallic (aluminium, for instance) and hence only needs to be silver-plated as a regular device machined out of an aluminium block.
On the other hand, polymer-based AM produces lighter components and very accurate dimensions, while ceramic-based parts benefit from low-loss/high-permittivity dielectric materials. However, metallisation of dielectric-based parts and their inner waveguides is not an easy task, and alternatives have been proposed based on sputtering or electroless plating.
Regardless of building material, there are some critical points in AM that have to be resolved in the coming years if AM is to become a realistic manufacturing method and traditional computer-controlled machining is to be put aside, not only for structural parts in the satellite where AM is already a reality, but for RF/microwave components too.
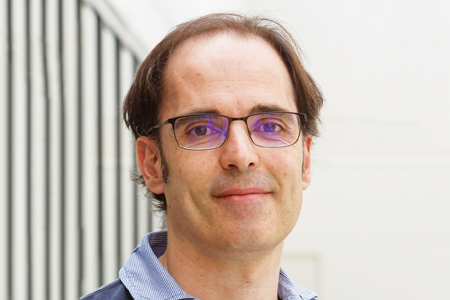
Geometric accuracy, surface roughness, high power, high temperature and mechanical behaviour, as well as general behaviour in space conditions, plating, etc, are just a few of the challenges that AM faces, according to the RF/microwave community. This is an opportunity for electrical engineers to work closely with mechanical and material engineers and develop low-cost, low-weight, accurate procedures when thousands of small satellites are manufactured for big data/sensor IoS constellations.
Broader bandwidth communications and the integration of IoS sensor services over the same satellite network seem to demand increased operating frequency for increased capacity and functionality. For RF/microwave components, increasing the frequency comes at a price. Manufacturing devices at millimetre- and sub-millimetre-wave ranges becomes increasingly difficult using traditional methods. Design methods able to withstand fabrication errors when the component arrives at the workshop are being proposed. These resilient components could then be fabricated at high frequencies at the millimetre-wave range, using the manufacturing methods of lower frequencies.
At sub-millimetre-waves, a different fabrication strategy has to be used. Some laboratories have opted for Deep Reactive Ion Etching (DRIE) micromachining, which etches 3D geometries in bulk silicon. The device is divided into several parts that, after being etched, are coated with a thin metal layer (at least 10 times the electrical skin depth at the operating frequency) and mounted.
SU8 is an alternative technology, cheaper than DRIE. However, Si is superior to SU8 in every physical, electrical and thermal aspect. There are also developments using very accurate micromachining of intricate 3D shapes. Not only the price, but also the repeatability and/or compatibility of all these techniques with space conditions are nowadays sometimes questioned.
Increasing capacity means increasing bitrate and accommodating a larger number of channels – hence the need for the satellite to handle higher combined signal powers. New classes of high-power filters, for instance, have been in the spotlight of both academic institutions and industry, and some proposals have been developed for increasing output power handling.
Passive Inter-Modulation (PIM) and multipaction are the main high-power phenomena associated with high-power RF satellite payloads. Multi-frequency and multibeam satellites make things even more complicated to design, simulate and test. Heat and heat dissipation pose challenges that engineers of high-power payloads have to face. New aluminium alloys with lower coefficients of thermal expansion would help, especially if parts can be additively manufactured and silver plated. The relationship between AM and high-power remains unexplored, with more research needed, as well as the development of specific space-oriented materials offering better heat dissipation.
Future satellite communications demand more flexibility, allocating resources when and where needed for global broadband access and integration with IoT. The technologies above are just some examples of what researchers in universities and research centres around the world are focusing on in terms of the RF/microwave passive components of future flexible payloads.
Some of these efforts are coordinated and it’s worth mentioning initiatives such as the TESLA-ITN network in Europe, which brings RF/microwave research groups together to find solutions to the challenges mentioned above.
Undoubtedly, at the pace at which our business is evolving, with so many inspiring and technically difficult projects in the decades to come, universities will have to work closely with industry to quickly respond to its needs, as well as with space agencies, putting many decades of theoretical work at the service of tomorrow’s challenges.
Our future space ecosystem seems to be characterised by the ubiquity of data and sensor information; low-cost development, testing and access to space; space as a marketplace; reconfigurability and flexibility; and immediate internet access to spacecraft data from every point of the planet.
Dr Miguel A. G. Laso is Associate Professor at the Public University of Navarre (UPNA), in Spain. He is also Head of the Microwave Components Group at UPNA – Institute of Smart Cities, and a member of the TESLA-ITN network.
Add Comment