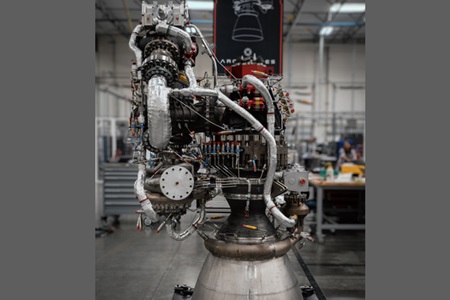
Rocket Lab has completed the first full assembly of its Archimedes engine, a 3D-printed, reusable rocket engine designed for the company’s Neutron medium-lift launch vehicle. The achievement marks the beginning of an intensive test campaign that will include a series of engine system activations leading up to the inaugural hot-fire test of Archimedes.
The rigorous Archimedes test campaign will be conducted at Rocket Lab’s dedicated engine test stand located at NASA’s Stennis Space Centre in Mississippi, America’s largest rocket propulsion test site. Archimedes, powered by liquid oxygen and methane oxidizer-rich staged combustion cycle, is a rocket engine renowned for its thrust class, engine cycle, and propellant combination. Engine design prioritises maximum reusability, operating at lower stress levels compared to other engines on the market, with a minimum reuse target of up to 20 launches per engine. Each Archimedes engine is capable of producing 165,000 lbf (733 kilonewtons) of thrust, totaling 1,450,000 million lbf on Neutron’s first stage. Key 3D printed parts to undergo testing include turbo pump housings, pre-burner and main chamber components, valve housings, and engine structural components.
The comprehensive test campaign encompasses various component, subsystem, and all-up system tests to validate Archimedes’ performance during start-up, steady-state, and shut-down phases. The engine test and development initiative significantly contribute to the Neutron launch schedule, with the first launch now anticipated no earlier than mid-2025.
Peter Beck, Founder and CEO, Rocket Lab, said: “Having a completed Archimedes engine on the test stand is an inflection point in Neutron’s development programme. Now we’ve entered the home stretch where we breathe fire and refine the engine in preparation for the first flight. Often with engine development plans, there can be a rush to get a minimum viable product to the stand, after which you have to spend years in redesign and iterative testing to get the performance you need, let alone being able to reproduce it reliably on a large production scale. What we’ve taken to the test stand is very close to a flight-like engine, and with all of our production infrastructure stood up alongside the engine’s development, we’re in a prime position to be able to make quick iterations to Archimedes for rapid development and qualification campaign. We took the time to not only bring a mature design to the stand that has been thoroughly tested at the component level, but to also stand up the experienced team, manufacturing line, and test facilities required to support the long-term production of Archimedes. This approach has ultimately pushed the first flight to mid-2025 at the earliest, but it’s an approach we believe will deliver the frequent flight rates the market needs quickly after flight one. Designing a brand-new rocket engine to meet the market demand for frequent and reliable launch is a complex feat, but it’s something we’ve successfully done before, having launched more than 470 Rutherford engines into space. We look forward to repeating this success with Archimedes.”
Simultaneously, the production of subsequent Archimedes engines continues alongside the ongoing test campaign. Long-lead 3D printed components are already in production, undergoing checks and analysis before integration and full assembly at Rocket Lab’s Engine Development Complex in Long Beach, California.
Recent achievements on the path to Neutron’s maiden flight include the completion of carbon composite flight structures for Neutron’s fairing panels, Stage 1 and Stage 2 tanks, and the reusable Stage 1 structure. Infrastructure development progresses rapidly at Neutron’s dedicated launch site in Wallops Island, Virginia, with completed foundation concrete works for Neutron’s launch mount, propellant, and gas storage facilities, as well as the installation of the site’s 278 ft water tower.
Add Comment